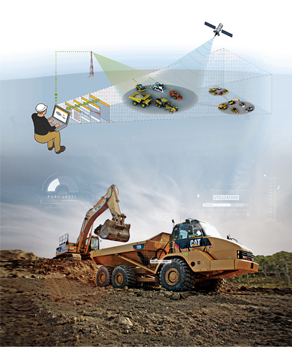
HAEIN Supports Customer’s Success with advanced Technical Skills, Information and Communication Technology as well as a step ahead Service.
HAEIN reduces operating costs and improves the growth of production by minimizing the suspension of the equipment service with the Vision Link system that checks the equipment condition in real time using satellite(GPS) and cellular networks, CVA that prevents malfunctions through preventive maintenance on a regular basis, and SOS service that responds to risk factors utilizing component oil analysis.
Introduction Video of EM Solution

-
Vision Link System
The Vision Link system diagnoses the equipment condition in real time with a device (Vision Link) attached to the construction equipment that sends various information to the web system(Vision Link) via satellite(GPS) and cellular networks, such as the location of the operating equipment, hours of operation, fuel consumption, hours of operation and idling, and abnormal status.
With VisionLink, you can easily access the various types of information transmitted by ProductLink anytime, anywhere—via both the website (PC version) and the mobile app. This enables you to proactively prepare for potential risks that may affect your equipment.
HAEIN manages the equipment efficiently and minimizes operating costs by providing analysis data on a regular basis that can increase work efficiency and productivity as well as consumables replacement and maintenance period of each customer, by analyzing the data extracted using the Vision Link system.
-
CVA Service (Equipment Management Contract)
The CVA service enhances productivity and minimizes costs and suspension of the service caused by malfunctions, by keeping the product in an optimal state all the time by providing regular and systematic diagnosis, preventive maintenance, and inspection service for the construction equipment, engines, and generators provided by HAEIN.
When the CVA service is used, the equipment can be operated more efficiently, and effective budgeting and cost savings are possible owing to the regular visits by CVA experts, advance diagnosis through oil analysis, and quick repair and operation consulting.
In addition, the equipment service life can be extended by using genuine parts that are optimized for Caterpillar equipment and engines, and high used equipment value can be guaranteed through systematic equipment history management.
-
SOS Service (Scheduled Oil Sampling)
The SOS (Scheduled Oil Sampling) service diagnoses the equipment condition by collecting oil from major parts(engine, transmission, final drive, differential gear, etc.) regularly that are in operation. Customers can minimize the suspension of the equipment service and reduce repair costs by preventing equipment failure, by taking preemptive action against risk factors (abrasion of component metals, oil contamination, etc.) using this service.
HAEIN provides additional professional services by commissioning Caterpillar oil analysis to a specialized institute in China (Shanghai S.O.S Lab) and manages the equipment more efficiently and cost-effectively by providing equipment condition reports through oil analysis on a regular basis.
Equipment Management Solution 5 Steps
-
01 Connection
Once connected to the Caterpillar Vision Link system, the equipment condition information (location, hours of operation, fuel consumption, and consumables replacement time of equipment in operation) as well as equipment health condition (oil replacement period and contamination state) can be checked in real time at anytime and anywhere.
-
02 Notification
Monthly operation status reports are sent to customers by analyzing the data extracted using the Caterpillar Vision Link system in detail, so that customers can understand the hours of equipment operation and suspension of the service, fuel consumption, and work efficiency at a glance. The competitiveness of holding equipment can be improved as it can be compared with equipment operating in a similar working environment.
-
03 Advice
CAT equipment management solutions can diagnose and improve customer’s driving habits and problems in the driving method, and minimize maintenance costs by informing abnormal symptoms and possible risk factors in the future, so that the customer can cope with the risk.
-
04 Support
HAEIN prevents the abrupt suspension of the equipment service and guarantees high used equipment value, by conducting preventive maintenance and component replacement by having the control plan document for component management and maintenance service available at all times.
-
05 Management
HAEIN supports continuous customer success by providing a 5-phase systematic and reliable management solutions, so that customers can concentrate on their own business after entrusting all management work to HAEIN
-
Optional/Required Items of the CAT Equipment Management Solution
Essential
Option
Item | 01 Connection | 02 Notification | 03 Advice | 04 Support | 05 Management |
---|---|---|---|---|---|
Installing and using Vision Link | ![]() |
![]() |
![]() |
![]() |
![]() |
Installing, connecting, and training of Vision Link | ![]() |
![]() |
![]() |
![]() |
![]() |
Ordering component on the Caterpillar online store | ![]() |
![]() |
![]() |
![]() |
![]() |
Equipment condition report (productivity, operational state, fuel use rate, repair, maintenance costs, etc.) | ![]() |
![]() |
![]() |
![]() |
![]() |
Comparative analysis of the operational state with the equipment used in a similar working environment | ![]() |
![]() |
![]() |
![]() |
![]() |
Installing, connecting, and training the SIS (Service Information System) | ![]() |
![]() |
![]() |
![]() |
|
Vision Link data, notification service, event | ![]() |
![]() |
![]() |
![]() |
|
Analysis using the HAEIN regular oil analysis (S.O.S) service | ![]() |
![]() |
![]() |
||
Long-term equipment examination | ![]() |
![]() |
![]() |
![]() |
![]() |
Repairing equipment and maintaining management records | ![]() |
![]() |
![]() |
![]() |
![]() |
Continuous monitoring of the equipment status | ![]() |
![]() |
![]() |
||
Accurate data analysis service | ![]() |
![]() |
![]() |
||
Accurate diagnosis of expert | ![]() |
![]() |
![]() |
||
Appropriate preventive maintenance | ![]() |
![]() |
![]() |
||
Technical support and continuous management | ![]() |
![]() |
![]() |
Contact Us
- CI & RI CVA Business
-
DH. Lee, CI & RI CVA Manager : dh_lee@haein.com
Paul. Kim, CI & RI CVA admin : er_kim@haein.com
- E&T EP CVA Business
-
KM Kim, EP Aftermarket Service Team Manager : km_kim@haein.com
- E&T MP CVA Business
-
Edward ju, MP CVA manager : ed_ju@haein.com